The value of a centralized digital logbook system
30 June 2021
As featured in the Summer 2021 edition of BIC Magazine’s digital publication.
Safety best practices in asset-intensive industries dictate that events occurring during shifts and the resulting actions taken as a result of those events be recorded, tracked and analyzed in a document commonly called a “shift logbook.” The shift logbook is, in many cases, the central repository that consolidates all the activities from many different sources, recording what happened during a shift. At the end of a shift, the logbook is used to help retrieve, then efficiently and accurately communicate and discuss critical information between the incoming and outgoing teams. The communication method as well as the type of information shared at shift handover can differ significantly between plants and even between departments of the same facility. Omitting information or even sharing inaccurate or incomplete information during handover have often been reported as contributing factors to catastrophic accidents. Therefore, the need to define a robust, efficient and consistent process, along with implementing an easy-to-use and effective shift logbook system, is imperative.
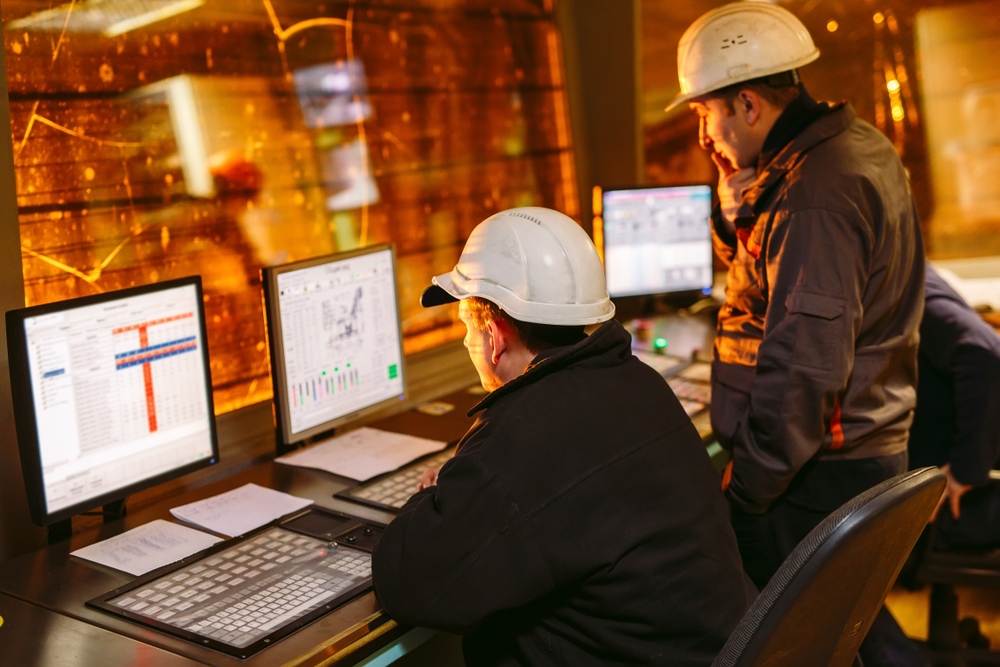
Common standalone solutions such as paper, spreadsheets or even local databases have been and are still being used in many facilities. These solutions provide limited data access for plant personnel, are susceptible to inconsistent or inaccurate entries due to lack of control standards, and in some cases, offer limited information search and retrieval due to limited capabilities or poor design.
Fortunately, as with many areas of plant digitization, transitioning from older forms of shift logs to electronic shift logs is becoming increasingly popular. Many factors contribute to the adoption of a digital logbook system. The advance of technology, including application interfaces and expanded Wi-Fi coverage; a younger generation of tech-savvy users; and added emphasis on plant efficiency, productivity and safety lead more and more companies to consider a centralized, digitized shift logbook.
Digitized shift logbooks that integrate with other plant operations management applications bring many advantages over manual or electronic standalone systems in the areas of consistency, standardization, accessibility, visibility, traceability and communication — all resulting in enhanced safety and productivity.
Once the decision is made to replace an older and sometimes manual logbook system with a centralized, well-integrated digitized solution, it is time to define the system requirements. See our guide below to help you select a professional, well managed Digital Logbook system.
Eight essential criteria and features of a professional digital logbook system
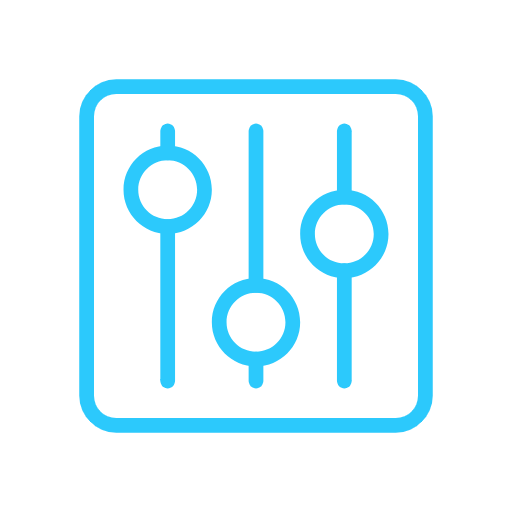
1) An easy-to-use setup option to;
- Define different types of logbooks
- Define data entry and workflow associated with the defined type of logbook
- Define the characteristics and rules associated with the defined type of logbook
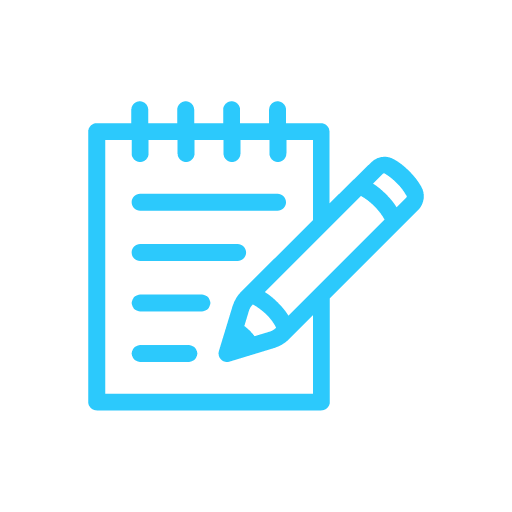
2) A flexible way to record events and activities with;
- Classification and tagging of entry logs
- Ability to enter freeform comments
- Use of standard entries
- Entry-sharing ability between logbooks.
- Recurring entry capability for repetitive entries (standard or template entries)
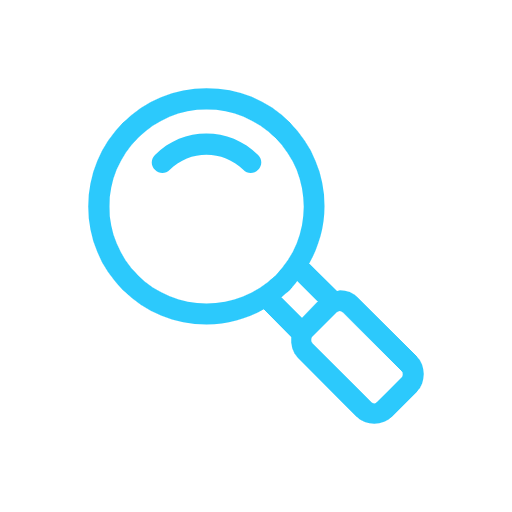
3) Powerful search and retrieval options
4) Shift manning management options
5) Shift data recording options
6) A shift handover management option to allow for;
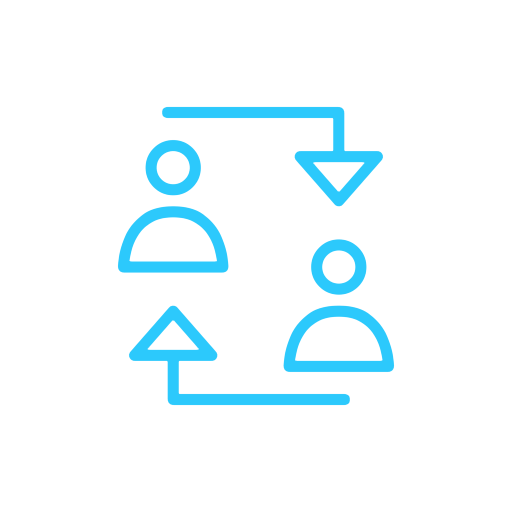
- Filtering entries
- Position handover
- Log handover
- Log approval
- Distributing electronic shift log information automatically
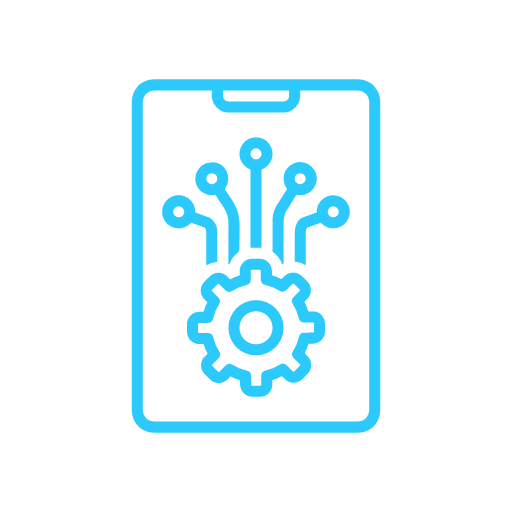
7) A system of rights to manage user/group authorizations
8) An integration with other applications such as permit to work, LOTO, data historian and procedures
Successful implementation of an effective digitized shift logbook requires sufficient and adequate training as well as support and buy-in from all plant personnel, including operators, maintenance, engineers and management. Information retrieval and usage is only as good as the quality of the information recorded.
For more information about customer implementations and product information, visit www.nisoft.com. NiSoft’s eclipseSuite software solution provides over 500 sites worldwide with enhanced compliance, visibility, control and communication across a range of operational documents and processes. With modules such as ePTW, eLOTO, eRISK and eLOG, NiSoft provide a comprehensive solution to your company safety and operational process management.
Contact NiSoft for a demo of the eclipseSuite using the form below;